Standford university researchers have published a new method of photopolymerization process which will make resin printing 5-10x times faster than the ones currently available in the market with high resolution
Basically the Continuous Liquid Interface Production (CLIP) was developed by Carbon3D, and this newest approach is iCLIP which is developed by the team in Stanford
What is the Difference between CLIP & iCLIP?
The key difference between CLIP and iCLIP is represented here: iCLIP utilizes a continuous liquid interface—the dead zone—mechanically fed with resin at elevated pressures through microfluidic channels that are dynamically created and are integral to the growing part
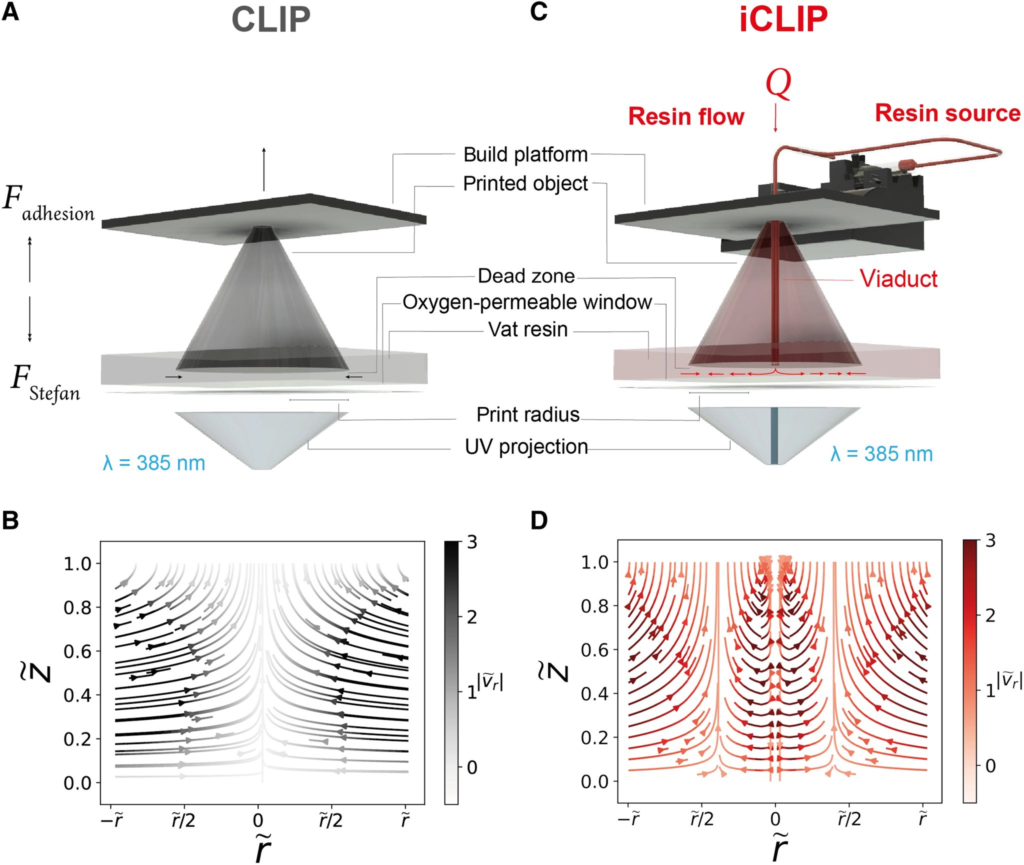
According to Joseph DeSimone, a co-founder of Carbon and one of the study’s authors, “this new technique will help us fully realize the potential of 3D printing.” It will make printing more faster and enable the creation of complicated, multi-material products in a single step, ushering in a new era of digital manufacturing.
Shaping up with CLIP’s dead zone
When CLIP 3D printing was originally released in 2015, it was co-developed by DeSimone and patented by his company Carbon. It is a type of photopolymerization technique, however it functions slightly differently than SLA or DLP. The method provides for the balance of UV light interactions, in a way that permits items to be continually “grown” from a resin pool, via a considerably faster process, as opposed to printing layer by layer.
According to one of the study’s other co-authors, Gabriel Lipkowitz, “the resin flow in CLIP is a fairly passive process – you’re essentially dragging the thing up and hoping that suction can transport material to the place where it’s needed.” With this revolutionary technology, resin is actively injected into the printer’s necessary locations.
The core of the CLIP method is a dead zone in the resin pool that is ten microns thick and prevents photopolymerization. The material is effectively projected with cross-sectional photographs of a 3D model above this window, hardening it into the appropriate forms. As a solidified piece rises, liquid resin is meant to fill in behind it, enabling smooth, continuous curing.
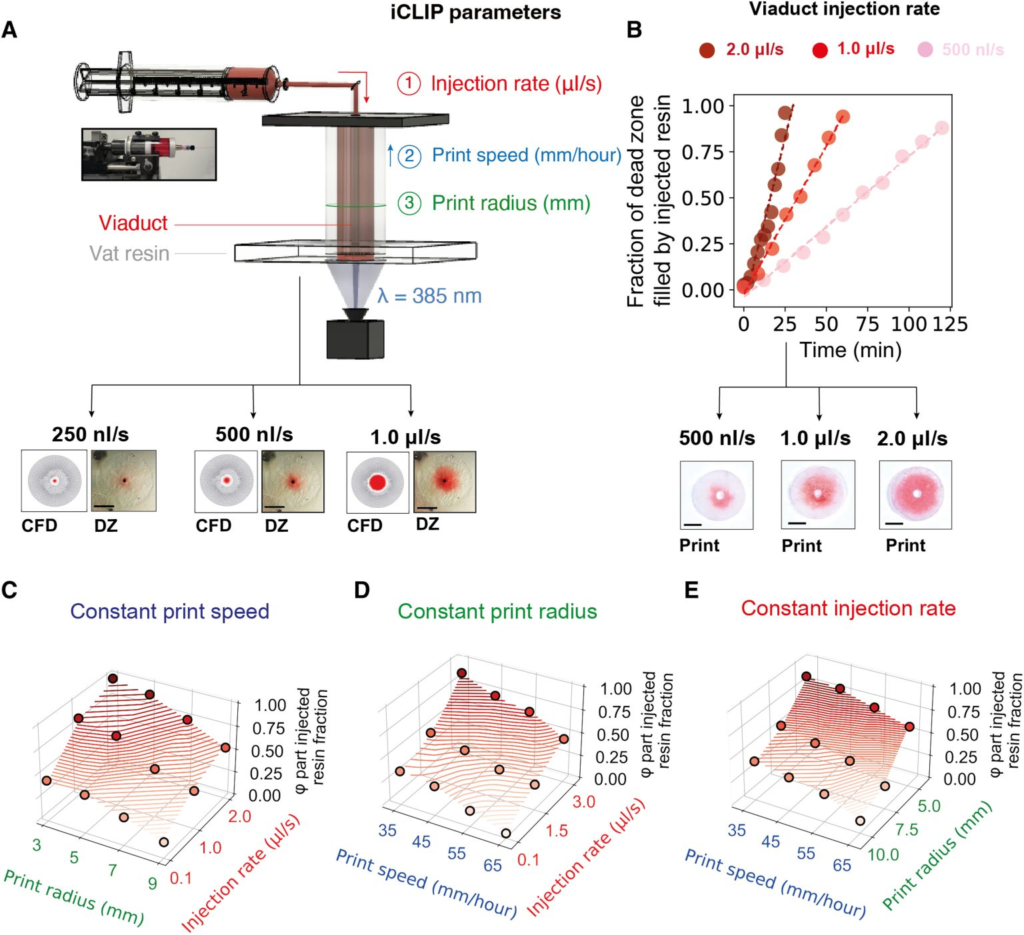
Multi material printing by iCLIP approach
The extra resin pumped into iCLIP builds is delivered via conduits that are printed with part designs. The Stanford scientists have found that incorporating vein-like channels into builds unlocks unique parts.
The team also hypothesized that iCLIP would make it possible to introduce multiple types of material during printing by injecting each additional resin separately. Scientists fitted a prototype system with three syringes, each with a different dye-colored resin, before using it to 3D print test models of famous buildings.
iCLIP Boosts Productivity and Reduces Defects
The team saw “viscous fingering” while they were working, which is a problem that happens when there are low and high-viscosity resins interacting. However, they say that this can be fixed by being careful about where the syringe is positioned. As a result, given that the efficacy of iCLIP has been demonstrated, the scientists are currently working on a program that will optimize the fluid distribution network of each component and further accelerate the process.
Lipkowitz concludes: “Designers shouldn’t be required to understand fluid dynamics in order to print an object extremely fast.” It’s an efficient program that generates the distribution network for a part that a designer wants to print and also determines the flow rates for different resins to achieve multi-material prints.”
Highlights of Carbon3D
Carbon3D has evolved in to a leader in the resin printing segment with major brands adopting their technology to improvise digital manufacturing and fastrack their innovation capabilities.
For example Adidas have started using their machines for soles production which has astounding benefits