In a move by RTA (Road and Transport Authority,
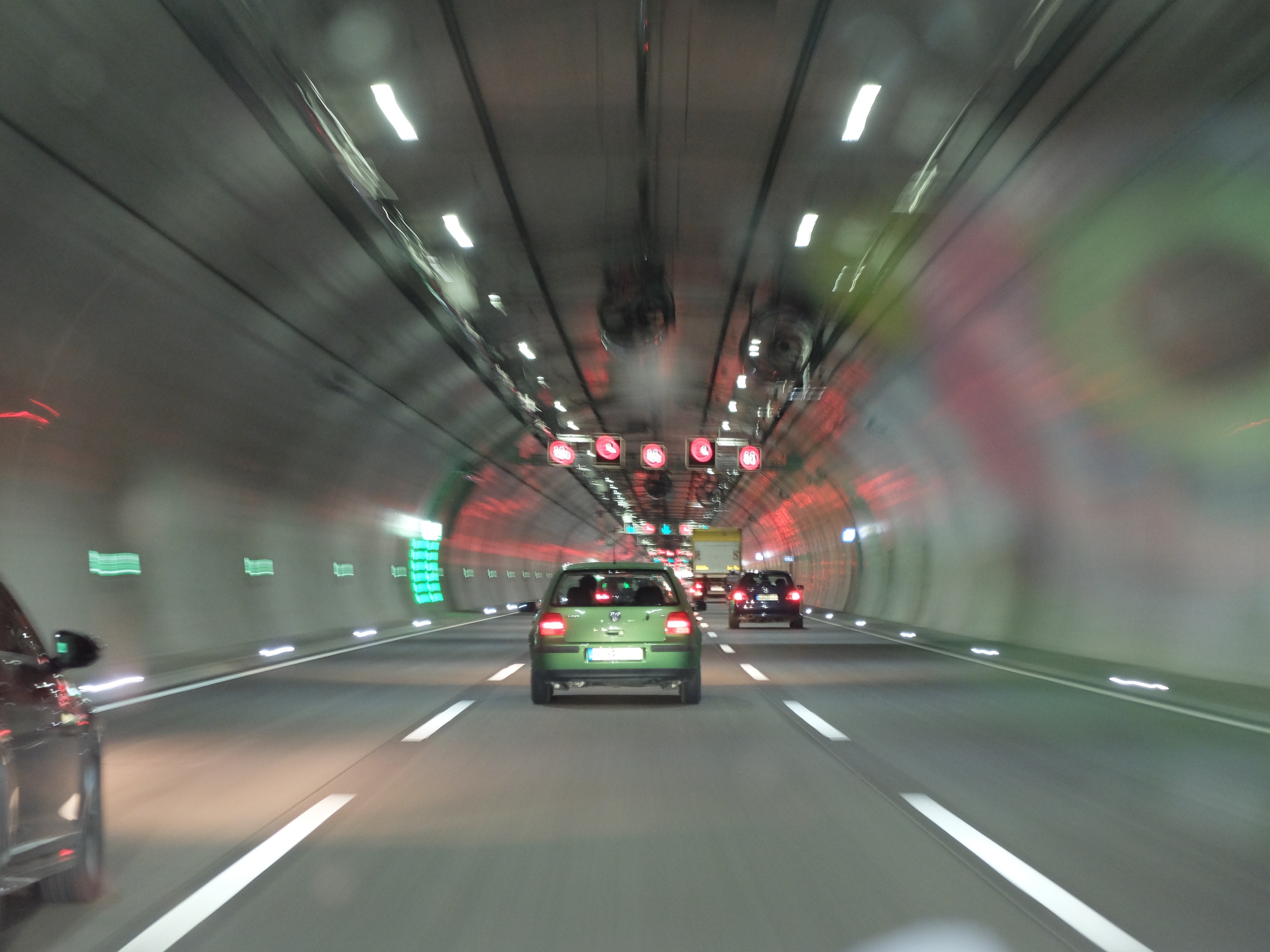
Additive manufacturing is gaining a lot of interest, and we have seen its uses in rail and other mobility services industry. However, road maintenance is something new application. Dubai Road and Transport Authority has recently proposed its move to adopt 3D printing in the improvement of road maintenance. RTA has partnered with experts in 3D printing in related field to accelerate and cater the special needs in this segment.
Together RTA and three other companies who are experts in additive manufacturing to jointly develop solutions, design parts and pavement utilities which are highly reliable and cost effective for road maintenance. Above all, additive manufacturing caters the problems in this segment quickly, efficiently and efficiently.
By adopting 3D printing RTA is demonstrating its desire to innovate new optimized technologies into its current process.
Maitha bin Adai, Executive Director of the Roads and Transport Authority, comments… “During the past few months, RTA developed a new initiative and conducted various studies and experiments to increase the availability of spare parts for roads maintenance systems, in cooperation with specialist 3D printing companies. The initiative has proved to be successful in extending the sources of spare parts such as propeller fans, control equipment, and cladding for tunnel walls in Dubai’s road facilities.”
3D Printing for Road maintenance and Pavement utilities:
As such in many situations, 3D printing has provided RTA with huge savings. RTA has reduced the cost of spare parts by upto 50% with the adoption of additive manufacturing. Designing and production of parts locally has a huge advantage over the lead time, this increasing the production rate and helps in reducing the cost of import from other countries.

RTA’s Executive Director also added “As part of the initiative selected types of spare parts were chosen to be 3D printed; based on specific criteria, such as the lack of spare parts in local markets and taking into consideration safety measures. The initial results of implementing the technology revealed a 50% saving in the operational cost of purchasing spare parts. Additional improvements were introduced on the factory-based spare parts on account of historical data analysis, which reduced breakdown rates to record-low levels. 3D printing technology also contributed to reducing the cost of transportation and the time needed to import spare parts to Dubai,”
In the initial stages RTA qualified the product lifecycle by validating the required quality parameters and standards. The spare parts to undergo necessary testing and qualification phase to be used in the real application.