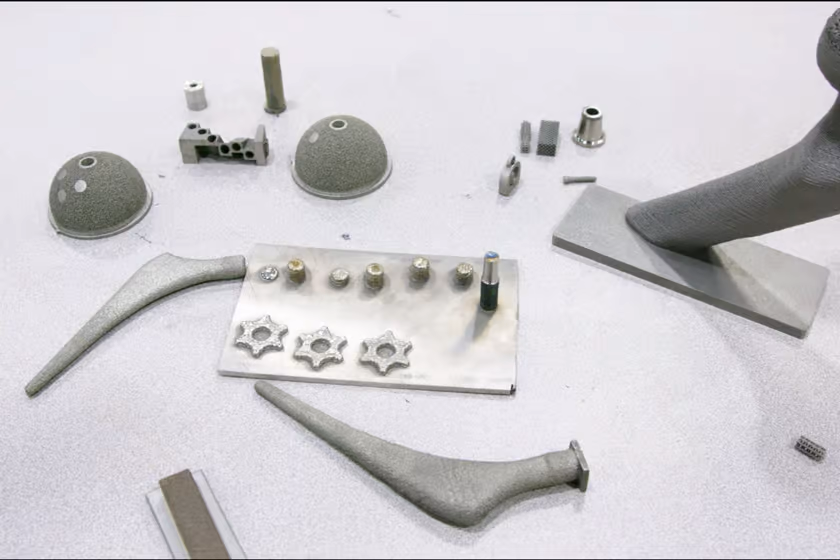
Sending substances into area is expensive, so the greater astronauts could make on-site, the better. Engineers at Washington State University (WSU) have now proven how overwhelmed Martian rock may be blended with a titanium alloy to make 3D-printable constructing substances. For the primary astronauts who will spend lengthy durations of time at the Moon or Mars, it`s now no longer truly an choice to simply duck right all the way down to the stores while you want constructing components or tools. Most of these substances will want to be dispatched from Earth at exquisite expense. Ideally, astronauts can be capin a position to utilize the sources round them – even though that`s frequently simply rock and dirt.
To that end, scientists were experimenting with approaches to make habitats, constructing materials, tools, components and different matters at once out of regolith, the rocky “soil” that covers the lunar and Martian surfaces. That ought to encompass making the preferred shapes the usage of three-D printers, high-powered lasers or focused daylight to soften the material, or compressing it into bricks. For the brand new study, the WSU researchers examined how Martian dirt could paintings while combined with a titanium alloy that`s regularly utilized in area exploration due to the fact it`s strong, light-weight and heat-resistant. Because they glaringly can`t get their palms at the actual thing, they used an synthetic substance designed to imitate the Red Planet regolith.
A high-powered laser heated the combined substances to temperatures over 2,000 °C (3,632 °F) to soften them. The crew then shaped this molten fluid into additives of various shapes and sizes, and cooled it right into a form of ceramic material. After it had cooled down, they examined its electricity and durability. The crew introduced exceptional quantities of regolith – 5, 10 and 100% via way of means of weight (wt%) – to the mix, and observed that the ensuing substances finished differently. Perhaps surprisingly, 5% grew to become out to be the most suitable amount, because it cooled with out cracking or effervescent and become observed to carry out higher than the titanium alloy alone, boasting greater than two times the hardness.
“This establishes that it is possible, and maybe we should think in this direction because it’s not just making plastic parts which are weak but metal-ceramic composite parts which are strong and can be used for any kind of structural parts,” said Amit Bandyopadhyay, corresponding author of the study.
The research was published in the International Journal of Applied Ceramic Technology. The team describes the work in the video below.